No matter how far you are from your nearest neighbor, if you live in the United States or Europe, UPS can deliver to your address. UPS can deliver to 80 percent of the planet within 48 hours, so if you live somewhere else, it's still pretty likely that UPS can find you to drop off or pick up packages. That's a lot of addresses -- and a lot of packages. In fact, in 2005, UPS delivered 3.75 billion packages and letters. That's more than one package for every two people in the entire world.
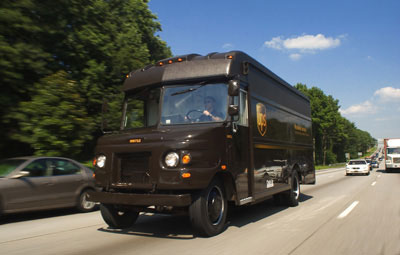
See more UPS pictures.
How exactly does UPS do all that? What does it take to get a package from one door to another in less than two days, even if that door is on the other side of the world?
It usually starts with pickup and ends with delivery -- every weekday UPS delivers more than 14.8 million packages and documents worldwide. But pickup and delivery are a tiny part of the process. The much bigger, more impressive, more complex step is the sort, which separates and organizes all those packages. It's entirely automated, and it turns one huge, random pile of packages into lots of small, organized piles.
To understand the sort, you need to know a little about what happens to a package before it gets to that step. So, imagine that three of your friends have moved to the other side of the United States. (If you live elsewhere, imagine that you live in the United States, too.) You want to send your friends a few gifts. One friend is getting a lightsaber in a box that's about 12 inches wide and 50 inches long. You've bought the second friend a LEGO Batmobile in a standard rectangular box. The third friend is getting a flat envelope containing a pair of tickets to see the One Man Star Wars Trilogy. To ship these packages via UPS, you can do one of two things:
- Go to the UPS Web site, enter all the necessary information about your packages, print out smart labels and schedule a pickup.
- Take your packages to the UPS store, where you or a UPS employee will enter the same information into a computer and print the necessary labels.
Either way, your packages will wind up bearing labels that have conventional bar codes and UPS maxi codes. Throughout the shipping process, machines and UPS employees can use bar-code scanners to read these codes and retrieve the information originally entered into the computer. This is why you can get real-time updates on where your packages are at the UPS Web site. The label also includes important information, like the delivery address, in print so that humans can read it. While not every package winds up with a smart label, more than 95 percent of the packages that travel via UPS do.
Once your packages have smart labels, they travel, usually by truck, to a local or regional sorting facility. There, employees scan the labels to determine where the packages need to go. If their destination is more than 200 miles away, the packages will travel by air -- less than 200 miles, and they go by truck.
Since your friends live on the other side of the country, your packages go into a cargo container. This container is large and domed so it can fit against the curves of the inside of an airplane. These containers can weigh as much as two tons. UPS employees can move them with minimal effort, though, since the airplane floors and airport concourses have built-in ball bearings and caster wheels on which the cans roll. This video will give you a glimpse of the ball-bearing floors in action.
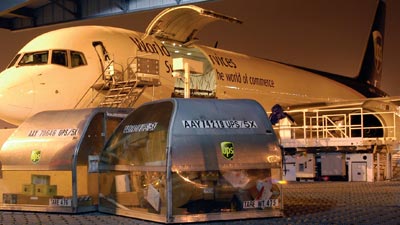
Advertisement